Choosing Appropriate Technologies
2. For Forms
I looked for a mechanised making process which would enable non-circular forms to be made. I decided that it was essential to find a mechanised process which has the potential to allow interventions during the making.
The Ram Press
 |
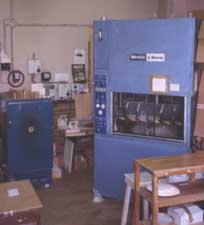 |
|
In my studio at Chapter Arts Centre, Cardiff – 8 cu. foot electric kiln on the left and my Simkin & Son Ram Press on the right. |
|
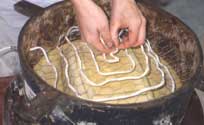 |
|
Metal die ring over model with chicken wire suspended above the model and nylon "purge pipe" being woven into the chicken wire. |
|
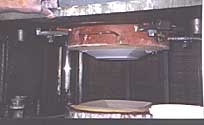 |
|
Clay dish stuck to upper die mould, ready to be removed with compressed air onto a ware board. |
|
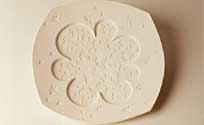 |
|
Ram pressed plate from my first model with 1 mm. rubber plotter-cut stencils of broccoli stem pattern. |
I selected the hydraulic ram press as the ideal industrial means of production. This machine raises and lowers a metal plate which has the top mould, or "die", attached. The bottom die is placed directly below the top die mould. These "dies" are not conventional plaster moulds. They have thick metal casings and are made from alpha plaster which has been made porous. When a model is being cast into a die mould, the metal ring is placed over the model, then chicken mesh is put into the die so that it hovers approximately one inch above the model. Hollow nylon tubing, called "purge pipe", is now threaded through a hole in the wall of the metal die and then carefully woven into the chicken mesh trying to prevent the tube from becoming closed off by sharp corners. When the alpha plaster is poured into the die it is checked for the rise in temperature as the plaster goes off. A compressed air hose is attached to the end of the purge pipe through the hole in the metal die. Compressed air is forced through the purge pipe and then into the plaster thereby making the alpha plaster porous. The porosity of the plaster enables plastic clay to be released from wet die moulds after pressing due to compressed air pushing through the moulds as part of the ram press cycle of making.
The ram press cycle
Place plastic clay into the bottom die mould; press the start button; a safety guard screen comes down; the top die is lowered down and presses the plastic clay into the mould; compressed air is pumped through the wet bottom die , pushing the clay off of the bottom mould and it then is stuck to the top mould; the top plate with the upper die mould with the plastic clay stuck to it now moves up, as does the guard screen; the operator places a board under the top die and steps on a foot pedal which sends compressed air through the top die mould which releases the plastic clay from the top mould and it drops onto the board.
What ram press to use
I had visited manufacturers with ram presses and had considered trying to work from one of these sites. Wedgwood, Spode, Wades in Stoke-on-Trent, plus a more local maker, Canon Hill Pottery just 5 miles from Cardiff were all possibilities. There would have been a charge to cover time on the ram press, clay used, plus bisque firing. I intended to glaze and glaze fire from my own studio. At first this option was very appealing, but I knew that I worked best within my own work space without tight time pressures and I was also concerned by the cost.
My second mortgage was put to good use as I managed to track down a second hand ram press. It was installed and set up in May 1999 when I also produced my first die moulds of my first dinner plate model.
Having my own machine was daunting at first, but it has given a much greater freedom than I would have had leasing a ram press. This freedom has already enabled me to explore adaptations within the normal ram press cycle. One of the most useful adaptations came from swapping the compressed air hoses from the top and bottom dies. This enables multiple pressings of the same piece before it is removed from the die moulds. With two pressings rather than one, each ram pressed piece can be given individual surface detail.
Of course you could put the details on the original model, including using the plotter-cut stencil shapes glued to the model. Each ram pressed piece would then be identical, as in industry, but I am interested in exploring the potential for the ram press to be used in a studio setting, producing one off or limited series pieces.
|